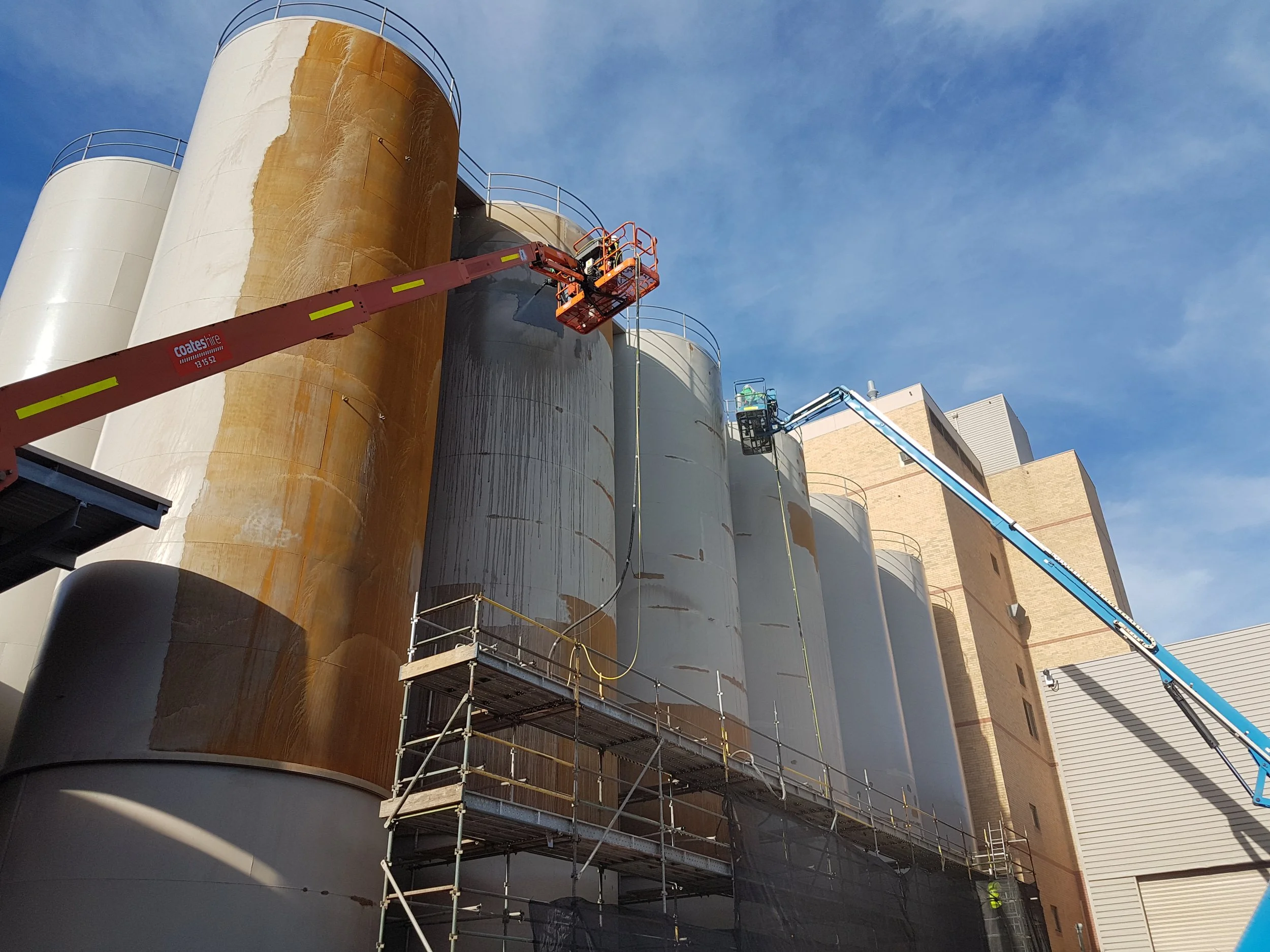
Surface Preparation & Abrasive Blasting
We utilise various surface preparation methods to remove existing corrosion and prepare substrates for protective coatings application. We are constantly innovating in the surface preparation service area to ensure that we have a wide range of fit-for-purpose surface preparation capabilities to reduce safety and environmental impacts, including robot operations and environmentally friendly alternatives.
Abrasive Blasting
High volume surface preparation technology that has been the backbone of the industry for the last century.
Abrasive blasting using conventional abrasives such as garnet and metal shot/slag is still the most commonly utilised surface preparation method due to its relatively low cost, high production rate and simplicity.
We have an extensive fleet of mobile abrasive blasting equipment as well as an off-site blasting facility at our Wingfield (SA) facility. Production rates of up to 20m² per hour/per operator are achievable.
Key benefits:
Fast production rate
High quality end finish
Cost effective
Wet and Mist Blasting
Ideal for shipyards and other large asset projects where encapsulation is impractical.
Mist and wet blasting allow us to rapidly prepare surfaces in situations difficult or impractical to encapsulate. Wet and mist blasting both use specialised equipment to inject a liquid element to the traditional abrasive blasting process, assisting in the suppression of airborne contaminants.
Key benefits:
Fast production rate
Suppression of airborne contaminants
Reduced requirements for containment minimising both time and cost
Aids in the removal of surface contaminants (salts and chlorides)
Dry Ice (CO2) Blasting
Clean food grade and electrical componentry with no residue, liquid or abrasive left behind.
Dry ice can effectively clean surfaces and recesses in a fraction of the time of traditional cleaning methods, which often include the risk of component and substrate damage. Dry ice blasting leaves no liquid waste as the ice turns immediately from a solid to gas. The process makes dry ice blasting ideal for usage in the food and beverage industry where contamination risk is high or where electrical componentry is nearby.
Key benefits:
Little to no downtime
Completely inert, non-toxic and incombustible
Safe to use over electrical components without risk of damage
Zero risk of contamination
No hazardous waste
Other operations may continue nearby (SIMOPS)
Medical grade cleaning capacity.
Sponge-Jet Blasting
A dry, low dust and reusable surface preparation method.
Sponge-Jet blasting is the world’s leader in clean, dry, low dust, reusable surface preparation. The heart of the Sponge-Jet system is its sponge media, in which abrasive particles are contained within pieces of sponge allowing the abrasive to come to the sponge’s surface and abrade on impact but then retract back into the sponge on reflection. This process traps almost all dust and debris (up to 99%) from the blasting process. Sponge media is then recycled through the fully integrated recycling system and can be re-used several times over, drastically reducing waste disposal requirements.
Sponge-Jet can be highly tailored to the project requirements by selecting from over 20 types of Sponge-Jet media, each having different effects. Sponge-Jet can be used for a wide variety of applications ranging from the delicate cleaning of heritage stone and fire-damaged structures right through to harsh corrosion removal and aggressive surface profiling.
Ultra High Pressure Water Jetting
Ideal for removing ultra stubborn substrates while leaving the base material undamaged.
Surface preparation via UHPWJ has many unique benefits and applications. Using only water at very high pressures (up to 40,000psi), a key benefit is the significantly reduced waste production.
Additionally, water jetting requires no management of respirable substances and provides a fast and thorough option for surface preparation including the removal of the most stubborn composites such as rubber lining.
Where the substrate has previously had a surface profile created in the past, UHPWJ can clean and present the previous surface profile, allowing new protective coatings to be applied directly over top of the water jetted surface without any need for re-blasting.
Soda Blasting
Fast and safe cleaning of delicate substrates without risking damage to surface finish or existing coatings.
Soda blasting can be used very effectively to remove grease, caked dirt, stubborn stains and paint from most surfaces. It is affordable and fast – it takes less than two minutes to blast a square foot of bare steel to a clean surface.
Soda blasting is a cost effective treatment for a wide range of surfaces. Importantly, it's just as good for cleaning organic materials made of wood and stone as it is artificial ones (such as steel). This versatility, aided by the ease of making the bicarbonate mix, means that soda blasting machines can be used in a great variety of cleaning roles.
By varying pressure and aggressiveness, soda blast can clean sensitively as therefore great for;
removing paint on thin substrates without generating excessive heat
Cleaning of porcelain and other sensitive materials without damaging surfaces